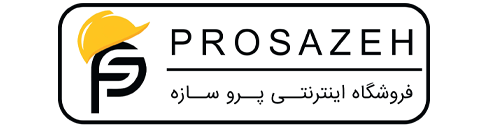
عیبیابی و تعمیر لولههای پلیاتیلن
عیب یابی و تعمیر لولههای پلیاتیلن
عیب یابی و تعمیر لولههای پلیاتیلن: لولههای پلیاتیلن در سالهای اخیر به دلیل دوام بالا، انعطافپذیری مناسب و هزینههای نگهداری پایین، به یکی از پرکاربردترین اجزای سیستمهای انتقال آب و فاضلاب تبدیل شدهاند. با این حال، این لولهها نیز مانند هر محصول صنعتی دیگر ممکن است در معرض آسیبها و مشکلات مختلف قرار بگیرند.
در این مقاله قصد داریم بهصورت تخصصی به موضوع عیبیابی و تعمیر لولههای پلیاتیلن بپردازیم، ابزارهای لازم را بررسی کنیم و چالشهای رایج در مسیر تعمیر و نگهداری را بشناسیم.
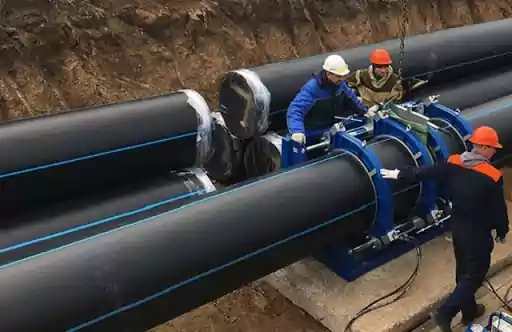
1. اهمیت لولههای پلیاتیلن در صنعت
لولههای پلیاتیلن در زمینههای مختلف نظیر انتقال آب آشامیدنی، خطوط فاضلاب شهری، آبیاری کشاورزی، انتقال مواد شیمیایی و … کاربرد دارند. مقاومت در برابر خوردگی، فشار و مواد شیمیایی، بههمراه خاصیت انعطافپذیری بالا سبب شده تا این نوع لولهها گزینهای ایدئال برای بسیاری از پروژههای زیرساختی باشند.
2. انواع آسیبها و علل آن
- ترکهای سطحی: در اثر تنشهای خارجی یا تابش نور خورشید بهصورت مستقیم و طولانیمدت ایجاد میشوند.
- نشتیها: معمولاً در محل اتصال یا جوش لوله پلیاتیلن به وجود میآیند.
- لهیدگی و تغییر شکل: برخورد وسایل نقلیه سنگین، خاکبرداری غیراصولی یا فشار بیشازحد از دلایل عمده این نوع آسیب است.
- سوراخشدگی: اغلب با ضربههای شدید یا حفاری اتفاق میافتد.
3. روشهای عیبیابی
عیبیابی و تعمیر لولههای پلیاتیلن با تشخیص بهموقع هرگونه نشتی یا ترک آغاز میشود. برای این کار میتوان روشهای زیر را به کار گرفت:
- بازرسی چشمی: اولین و سادهترین روش است که در آن لوله از نظر تغییر شکل، ترک یا نشتی ظاهری بررسی میشود.
- آزمون فشار یا تست هیدرواستاتیک: در این روش، لوله را با فشار مناسب پر از آب میکنند و با استفاده از گیج فشار و مشاهده تغییرات، نشتی یا ترک احتمالی بررسی میشود.
- تشخیص با دستگاههای الکترونیکی: حسگرها یا دستگاههای تشخیص نشتی، تغییرات فشار و صدا را ثبت میکنند و در صورت وجود مشکل، اطلاعرسانی مینمایند.
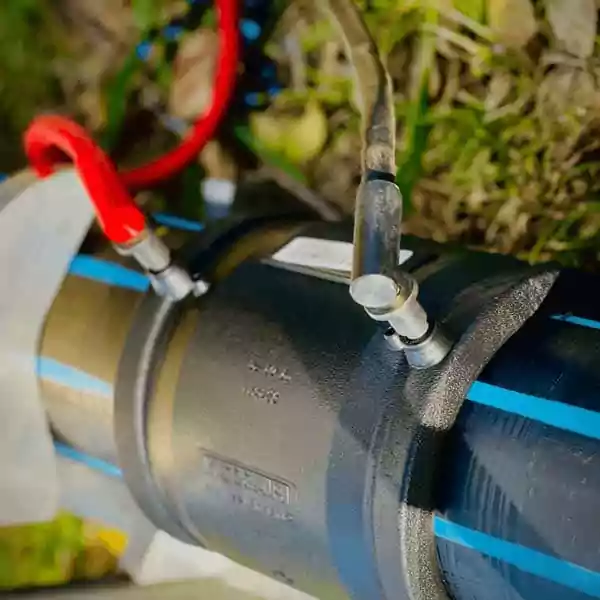
4. تجهیزات و ابزارهای مورد نیاز برای تعمیر
- جوش الکتروفیوژن: شامل دستگاه الکتروفیوژن، کوپلرهای مناسب و ابزار تمیزکننده سطوح لوله.
- جوش لببهلب (بات فیوژن): دستگاه جوش بات فیوژن، فک گیرنده لوله (Clamp) و تیغه برش لوله.
- ابزار برش و آمادهسازی: انواع کاتر یا اره مخصوص لوله پلیاتیلن، ابزار تراش لبه (اسکراپر) و وسایل تمیزکننده.
- ابزار ایمنی: دستکش، عینک ایمنی، لباس کار مخصوص و تجهیزات حفاظتی دیگر جهت کار با حرارت و جریان الکتریسیته.
5. روشهای تعمیر لولههای پلیاتیلن
جوش لببهلب
- مناسب برای لولههایی با قطر بالا.
- در این روش ابتدا دو سر لوله را با تیغه مخصوص کاملاً صاف و یکدست میکنند. سپس حرارت به دو انتهای لوله وارد میشود تا به نقطه ذوب برسد و با اعمال فشار کنترلشده دو سر لوله به هم جوش میخورند.
الکتروفیوژن
- در این روش از اتصالات کوپلر دارای سیم حرارتی استفاده میشود. پس از جایگیری مناسب لوله در کوپلر و اتصال سیمها به دستگاه الکتروفیوژن، حرارت ناشی از عبور جریان الکتریکی موجب ذوب شدن سطح لوله و اتصال آن به کوپلر میشود.
- این روش در فضاهای محدود و زمانی که جداسازی کامل لوله دشوار است، کاربرد بیشتری دارد.
تعمیر با استفاده از اتصالات فشاری (Compression)
- در برخی موارد که نیاز به جوشکاری یا حرارت نباشد، میتوان از کوپلرها یا اتصالات فشاری ویژه پلیاتیلن استفاده کرد که با سفت کردن مهره، لوله را آببندی میکنند. این روش عمدتاً در خطوط کمفشار و لولههای با قطر کوچک رایج است.
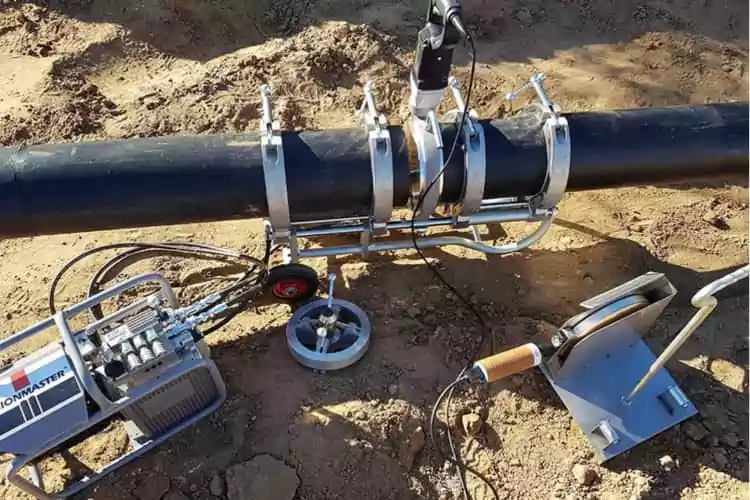
6. چالشهای رایج در عیبیابی و تعمیر
- دسترسی دشوار: در اغلب پروژههای عمرانی، لولهها در عمق خاک یا زیر جادهها قرار دارند. پیدا کردن محل دقیق نشتی در این شرایط کار دشواری است.
- تأمین تجهیزات تخصصی: دستگاه جوش الکتروفیوژن یا بات فیوژن هزینه بالایی دارند و برای پروژههای کوچک، اجارهکردن آنها بهصرفهتر از خرید است.
- نیاز به تخصص و مهارت: کاربر باید بداند فشار و حرارت را چگونه تنظیم کند تا کیفیت جوش بالا برود. کوچکترین خطا موجب نشتیهای مجدد یا آسیب به لوله میشود.
- کنترل شرایط محیطی: در دماهای بسیار بالا یا پایین، کیفیت جوش کاهش پیدا میکند؛ همچنین رطوبت هوا و آلودگی سطح لوله میتوانند مانع از اتصال مطلوب شوند.
7. استانداردها و نکات ایمنی
- رعایت دستورالعملهای تولیدکننده: هر دستگاه جوش پارامترهای خاص خود را دارد که باید طبق دستورالعمل اعمال شود.
- تمیزکاری سطح لوله: قبل از هر نوع جوشکاری، سطح لوله باید از هرگونه چربی، گردوغبار و رطوبت پاک شود.
- استفاده از ابزار ایمنی: عینک، دستکش و لباس کار مناسب باعث جلوگیری از سوختگی، الکتریسیته گرفتگی و آسیبهای دیگر میشود.
- بررسی فشار قبل از تعمیر: برای جلوگیری از بروز حوادث ناگوار، باید پیش از شروع تعمیر، فشار لوله را تا حد ممکن کاهش داد.
8. روشهای تست و اطمینان از صحت تعمیر
- تست هیدرواستاتیک
- پس از اتمام جوشکاری، لوله یا بخش تعمیرشده را با آب پر کرده و فشار معینی را در آن اعمال میکنیم. اگر فشار ثابت بماند یا افت کمی داشته باشد، نشتی وجود ندارد.
- بازرسی چشمی و تست نشتی با کف صابون
- در فشارهای پایین میتوان با استفاده از کف صابون دور اتصال و محل جوش را آغشته کرد. حباب نشاندهندهی نشتی است.
- آزمون با دستگاه نشتیاب
- استفاده از نشتیابهای دیجیتالی در پروژههای حساس و لولههای مدفون شده بسیار کاربردی است.
9. جمعبندی
عیبیابی و تعمیر لولههای پلیاتیلن فرایندی چندمرحلهای است که از تشخیص محل عیب و انتخاب روش مناسب جوشکاری گرفته تا بررسیهای دقیق بعد از تعمیر را در بر میگیرد. بهرهگیری از تجهیزات مناسب نظیر دستگاه جوش الکتروفیوژن یا بات فیوژن و رعایت استانداردهای لازم میتواند طول عمر خطوط انتقال و هزینههای نگهداری را به شکل چشمگیری کاهش دهد. از سوی دیگر، آشنایی با چالشهای احتمالی و پیدا کردن راهکارهای مؤثر، باعث میشود تا در کوتاهترین زمان ممکن مشکل برطرف شده و بهرهبرداری از سیستمهای آبرسانی یا فاضلابی بهسرعت از سر گرفته شود.